Amid the dual waves of global supply chain restructuring and fragmented consumer demand, SMEs and micro e-commerce businesses have long faced a common pain point: the “high minimum order quantity (MOQ)” threshold in traditional manufacturing. Order requirements often numbering in the thousands have barred countless innovative products from industrialization. However, as China’s manufacturing sector accelerates its digital transformation, a revolution centered on ”flexible production + single-piece distribution” is reshaping industrial logic, paving a low-cost, high-efficiency path for small and medium orders.
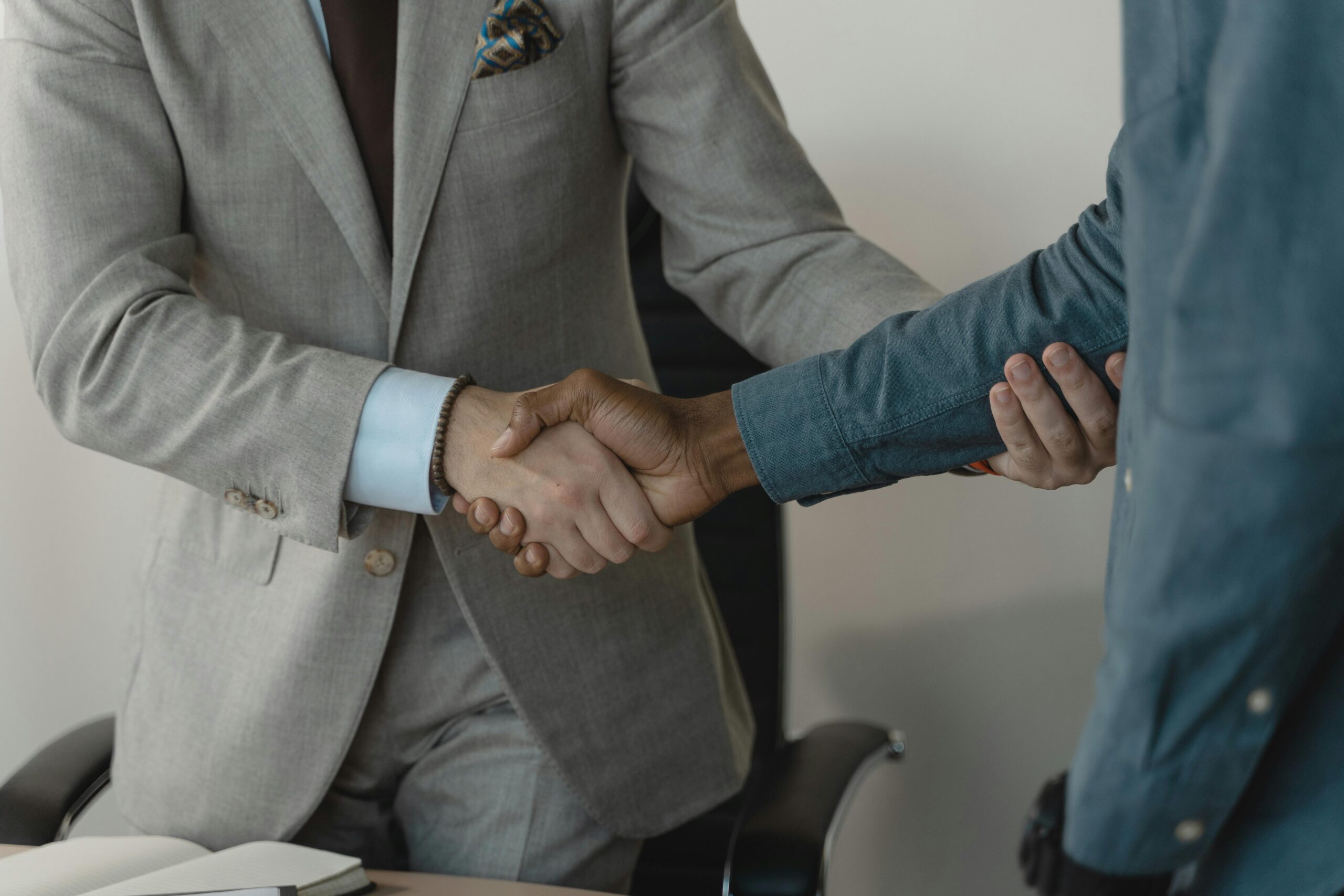
I. The High MOQ Dilemma: The “Scale Trap” of Traditional Manufacturing
Over the past three decades, Chinese manufacturing established its irreplaceable global position through economies of scale. Yet this very success formula has become an insurmountable barrier for small orders. Take cross-border e-commerce entrepreneur Wang Lei as an example: His smart pet feeder secured 2,000 orders on an overseas crowdfunding platform, but he hit walls across the Pearl River Delta region—factories demanded a minimum MOQ of 5,000 units, with mold development, raw material procurement, and production line setup costs rendering the project unviable.
This predicament reflects a deeper contradiction in traditional manufacturing: Standardized assembly lines rely on stable bulk orders to amortize costs, while fixed investments in mold development and production line adjustments create inherent barriers. Statistics show that the median MOQ in China’s manufacturing sector stands at 3,000 units. For cost-sensitive SMEs, this is akin to an unbridgeable chasm.
II. The Flexible Production Revolution: From “Rigid Lines” to “Smart Manufacturing Cells”
A breakthrough emerged with the application of smart manufacturing technologies. At a garment factory in Jiaxing, Zhejiang Province, traditional assembly lines were dismantled into dozens of ”micro production units.” Through modular equipment, a single workshop now handles 20 different designs simultaneously, slashing order response times from 45 days to 72 hours. Dubbed ”cellular production,” this model leverages industrial internet platforms for real-time production scheduling, ensuring profitability even for 50-unit orders.
The core innovations of flexible production lie in three dimensions:
- Modular Design: Products are broken into standardized components, enabling rapid innovation via parametric modeling.
- AI-Powered Scheduling: Algorithms dynamically optimize production plans for mixed-order processing.
- Rapid Line Switching: Magnetic molds and programmable robotic arms reduce line changeover times by 90%.

III. Single-Piece Distribution: Rebuilding Supply Chain “Capillaries”
If flexible production solves the “making it possible” challenge, ”single-piece distribution” addresses the “getting it sold” final mile. In Qingdao’s industrial belt, SMEs upload designs to platforms where systems auto-generate production requirements. Factories manufacture and ship directly to consumers, bypassing warehousing. This “zero inventory” model compresses seven traditional supply chain stages into three, reducing logistics costs by 40%.
Behind this lies a deeply integrated ecosystem:
- Cloud Factory Networks: Aggregate idle capacity from 3,000+ certified factories.
- Distributed Warehousing: AI-driven inventory algorithms based on demand forecasting.
- Real-Time Logistics Routing: Blockchain-enabled end-to-end traceability.
IV. Technological Foundation: Digital Empowerment via Industrial Internet
This transformation is rooted in the convergence of industrial internet, big data, and 5G. A Hangzhou industrial cloud platform reports that connected enterprises achieve 73% equipment connectivity rates and 32% faster order fulfillment. Key enablers include:
- Digital Twins: Simulate production processes to preempt scheduling conflicts.
- Dynamic Pricing Models: Real-time cost calculations based on order urgency and material fluctuations.
- AI Quality Control: Reduces inspection costs for small batches by 58%.
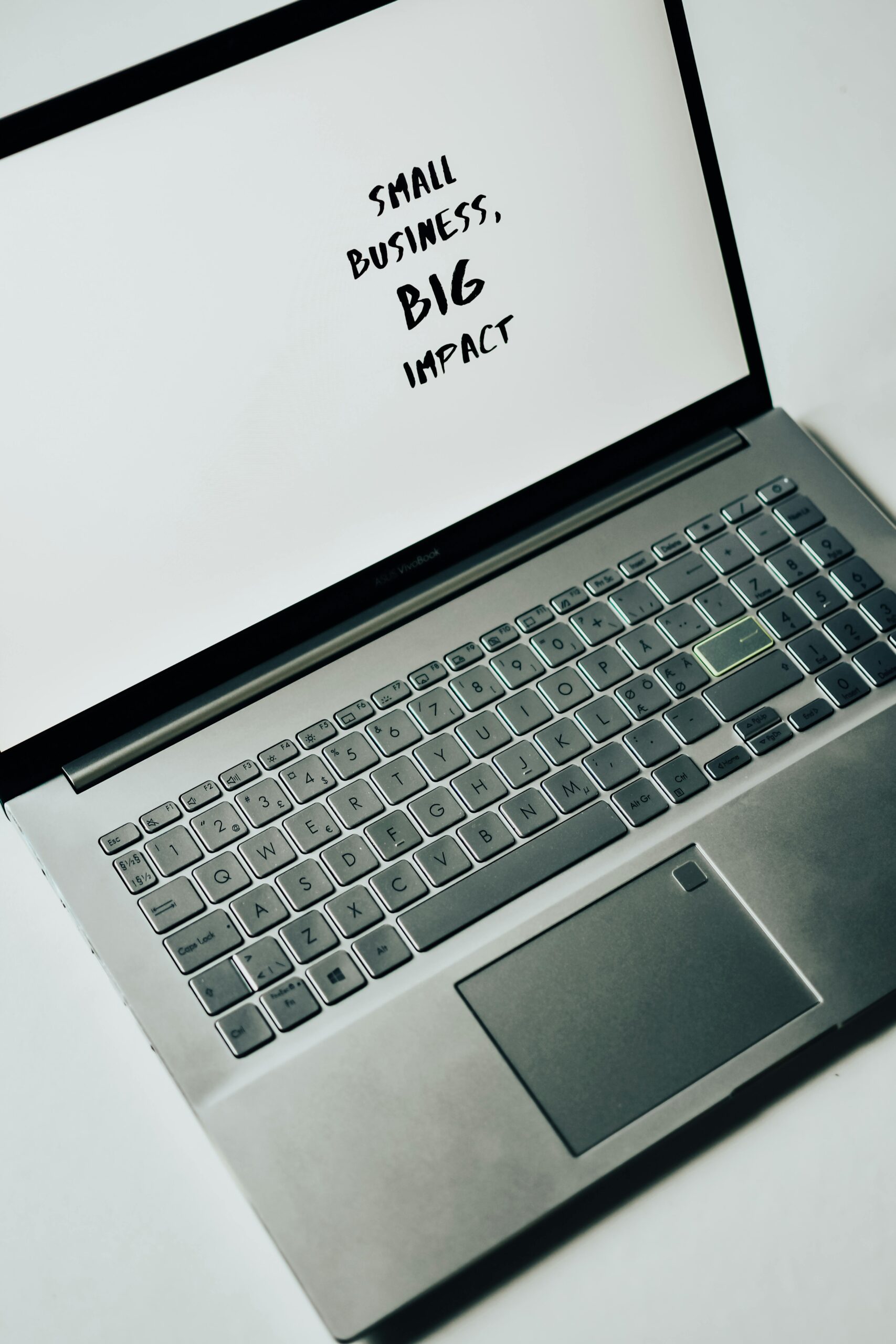
V. Industrial Transformation: From “Production-Centric” to “Demand-Driven”
This innovation is triggering systemic shifts:
Collaborative Ecosystems: Linear supply chains evolve into networked “design-production-logistics” ecosystems. A Dongguan furniture cluster cut product launch cycles from 90 to 7 days via shared prototyping centers.
Servitization of Manufacturing: Factories transition from pure production to “product + service” models. A Foshan home appliance firm now derives 35% of revenue from smart home solutions.
Democratized Innovation: Micro-entrepreneurs’ trial costs drop by 80%, while Yiwu’s small commodity market saw a 210% surge in new product launches in 2023.
VI. Challenges and Future: Bridging the “Scalable Customization” Gap
Despite promise, hurdles remain: Industrial internet upgrades average $280,000 with ROI periods exceeding three years for SMEs. Flexible lines consume 15-20% more energy, conflicting with decarbonization goals. Solutions include:
- Policy: Include flexible transformation in tech subsidies and establish industry standards.
- Technology: Develop lightweight SaaS tools to lower digital barriers.
- Ecosystems: Build cross-sector capacity-sharing platforms.
Conclusion: China’s Manufacturing “Second Growth Curve”
As “flexible production + single-piece distribution” becomes mainstream, Chinese manufacturing is rewriting its narrative—no longer relying solely on cost advantages but unifying scale efficiency with customization agility through digital reinvention. This shift not only unlocks opportunities for small orders but propels the sector from “physical competition” to “intelligent rivalry.” According to MIIT forecasts, flexible manufacturing will cover 30% of large enterprises by 2025, adding $1.2 trillion to industrial value chains. This quiet revolution may well be the key to China’s manufacturing sector navigating cycles and achieving high-quality growth.
No responses yet